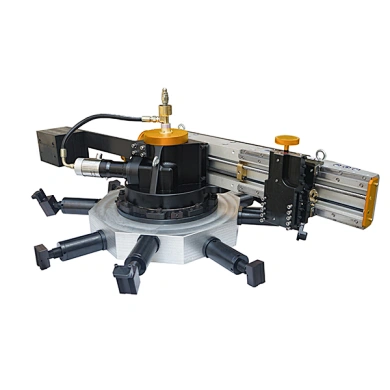
# Portable Flange Machining Tool for Oil and Gas Pipelines
## Introduction to Portable Flange Machining Tools
Portable flange machining tools have become indispensable in the oil and gas industry, offering a practical solution for on-site flange maintenance and repair. These specialized tools are designed to address the unique challenges of pipeline systems, where traditional machining methods are often impractical or impossible to implement.
## Key Features of Portable Flange Machining Tools
Modern portable flange machining tools offer several advantages that make them ideal for oil and gas pipeline applications:
– Compact and lightweight design for easy transportation
– High precision machining capabilities
– Ability to work in confined spaces
– Versatility for various flange sizes and types
– Reduced downtime compared to traditional methods
## Applications in Oil and Gas Pipelines
Portable flange machining tools serve multiple critical functions in pipeline maintenance:
### 1. Flange Facing
These tools can accurately machine flange faces to restore proper sealing surfaces, eliminating leaks and ensuring pipeline integrity.
### 2. Groove Cutting
Specialized attachments allow for precise groove cutting in flange faces for gasket seating.
### 3. Bolt Hole Repair
Damaged or misaligned bolt holes can be reconditioned on-site without removing the flange.
## Benefits for Pipeline Operators
The use of portable flange machining tools provides significant advantages:
– Cost savings by avoiding complete flange replacement
– Reduced system downtime during maintenance
– Improved safety by minimizing hot work requirements
– Extended service life of existing pipeline components
– Compliance with industry standards and regulations
## Choosing the Right Portable Flange Machining Tool
When selecting a portable flange machining tool for oil and gas applications, consider:
– Maximum flange diameter capacity
– Power source requirements (electric, hydraulic, pneumatic)
– Material compatibility (carbon steel, stainless steel, etc.)
– Environmental conditions (explosion-proof requirements for hazardous areas)
– Ease of setup and operation
## Maintenance and Safety Considerations
Proper maintenance and operation are crucial for optimal performance:
– Regular inspection of cutting tools and machine components
– Proper lubrication of moving parts
– Adherence to manufacturer’s operating guidelines
– Implementation of appropriate safety measures during operation
– Training for personnel using the equipment
## Future Trends in Portable Flange Machining
The industry continues to see advancements in portable flange machining technology:
– Integration with digital measurement systems
– Development of more compact and powerful units
– Improved automation features
– Enhanced materials for longer tool life
– Better adaptability to challenging field conditions
Portable flange machining tools represent a significant advancement in pipeline maintenance technology, offering oil and gas operators a reliable, efficient, and cost-effective solution for flange repair and maintenance. As these tools continue to evolve, they will play an increasingly important role in ensuring the safety and reliability of pipeline infrastructure worldwide.