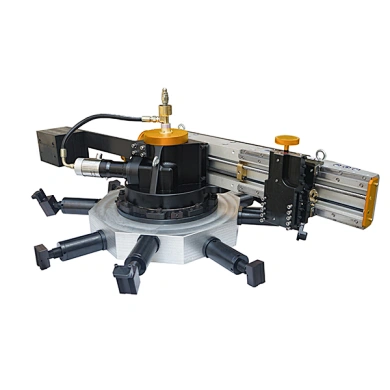
# On-Site Flange Machining Services
Keyword: On-site flange machining
## What is On-Site Flange Machining?
On-site flange machining refers to the process of repairing, resurfacing, or modifying flange faces directly at the installation location rather than removing and transporting the flange to a machine shop. This specialized service is particularly valuable in industries where downtime is costly or flange removal is impractical.
## Benefits of On-Site Flange Machining
The advantages of performing flange machining on-site include:
– Reduced downtime: Equipment can remain largely operational during the process
– Cost savings: Eliminates transportation costs and minimizes production losses
– Precision work: Modern portable equipment delivers machine-shop quality results
– Flexibility: Can be performed in challenging environments (offshore, confined spaces, etc.)
– Immediate verification: Flange performance can be tested right after machining
## Common Applications
On-site flange machining services are commonly used for:
– Power generation plants
– Oil and gas facilities
– Petrochemical plants
– Water treatment facilities
– Marine applications
– Heavy industrial manufacturing
## The Machining Process
The typical on-site flange machining process involves:
1. Inspection and measurement of the existing flange
2. Setup of portable machining equipment
3. Precise machining to restore flatness and surface finish
4. Verification of dimensional accuracy
5. Final inspection and quality assurance
## Equipment Used
Modern on-site flange machining utilizes specialized portable equipment including:
– Portable milling machines
– Orbital flange facers
– Lathe-style flange machines
– Grinding equipment
– Precision measurement tools
## Choosing a Service Provider
When selecting an on-site flange machining service provider, consider:
– Experience with your specific type of flange
– Equipment capabilities and precision
– Safety record and certifications
– Response time and availability
– Quality assurance processes
On-site flange machining provides an efficient solution for maintaining critical flange connections without the need for component removal. This service helps industries maintain operational continuity while ensuring proper sealing performance of their flange connections.