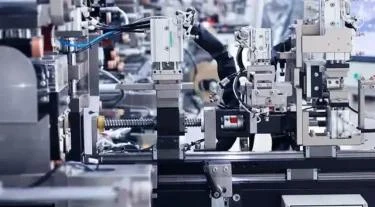
# Tape Manufacturing Process and Techniques
## Introduction to Tape Manufacturing
Tape manufacturing is a complex process that involves multiple steps to create various types of adhesive tapes used in numerous industries. From packaging to electrical insulation, tapes serve essential functions in our daily lives. The manufacturing process requires precision, quality materials, and specialized techniques to ensure the final product meets industry standards.
## Raw Materials Used in Tape Production
The foundation of any tape manufacturing process lies in the selection of high-quality raw materials. The primary components include:
– Backing material (paper, plastic, cloth, or foil)
– Adhesive (rubber-based, acrylic, or silicone)
– Release liner (for pressure-sensitive tapes)
– Additives (for UV resistance, flame retardancy, etc.)
## The Tape Manufacturing Process
### 1. Backing Material Preparation
The first step involves preparing the backing material. Depending on the tape type, this could involve:
– Extruding plastic films
– Weaving or knitting fabric backings
– Processing paper or foil materials
### 2. Adhesive Application
There are several methods for applying adhesive to the backing material:
– Direct coating: Adhesive is applied directly to the backing
– Transfer coating: Adhesive is first applied to a release liner, then transferred to the backing
– Hot melt coating: Adhesive is heated and applied in liquid form
### 3. Drying and Curing
After adhesive application, the tape goes through drying ovens or curing chambers to:
– Remove solvents (for solvent-based adhesives)
– Allow chemical curing (for reactive adhesives)
– Achieve proper tack and cohesion
### 4. Slitting and Rewinding
The large rolls of coated material are then slit into narrower widths:
– Precision slitting machines cut the material to specified widths
– Edge trimming ensures clean, uniform edges
– Rewinding creates manageable roll sizes for packaging
### 5. Quality Control and Testing
Throughout the manufacturing process, rigorous quality checks are performed:
– Adhesion strength testing
– Thickness measurement
– Tensile strength evaluation
– Visual inspection for defects
## Specialized Tape Manufacturing Techniques
### Pressure-Sensitive Tape Production
Pressure-sensitive tapes require unique manufacturing considerations:
– Controlled adhesive rheology for proper tack
– Release coating application on the non-adhesive side
– Precise tension control during winding
### Double-Sided Tape Manufacturing
Double-sided tapes present additional challenges:
– Simultaneous or sequential adhesive application
– Intermediate liner requirements
– Balanced adhesive properties on both sides
### Foam Tape Production
Foam tapes incorporate additional steps:
– Foam substrate preparation
– Specialized adhesive formulations
– Enhanced compression and recovery properties
## Environmental Considerations in Tape Manufacturing
Modern tape manufacturing focuses on sustainability through:
– Water-based adhesive systems
– Recyclable materials
– Energy-efficient production processes
– Waste reduction initiatives
## Future Trends in Tape Manufacturing
The industry continues to evolve with:
– Smart tapes with embedded sensors
– Biodegradable adhesive formulations
– Nanotechnology-enhanced properties
– Automated quality control systems
The tape manufacturing process combines material science, precision engineering, and quality control to produce versatile products that serve countless applications across industries. As technology advances, tape manufacturers continue to innovate, creating products with enhanced performance and environmental sustainability.
Keyword: tape manufacturing